Revolutionise your SPIR process with K:spir Reduce spare parts and warehouse management costs 30% reduction in unnecessary stock 60% reduction in spare parts management costs Reduction in spare parts supports sustainability initiatives Improve operational efficiency and financial performance
Transform your SPIR process, reduce the costs of spare parts and warehouse management with our cloud based, Spare Parts Lists and Interchangeability Record (SPIR) platform.
Benefit from real time spare parts analytics giving you total control and complete transparency over your SPIRs.
Data Collection made easy
Create and manage SPIR documents in a single cloud based platform
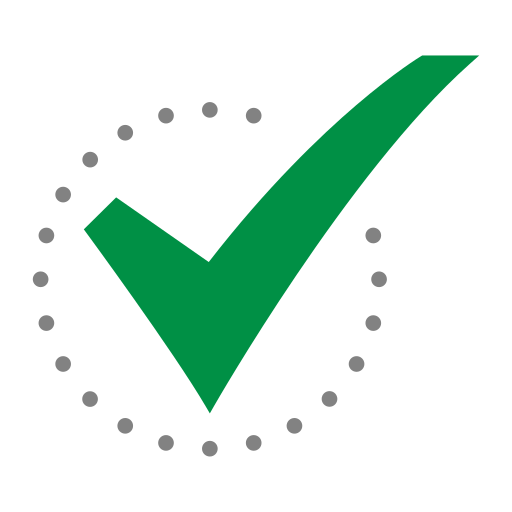
Eliminate management and data extraction from multiple spreadsheets
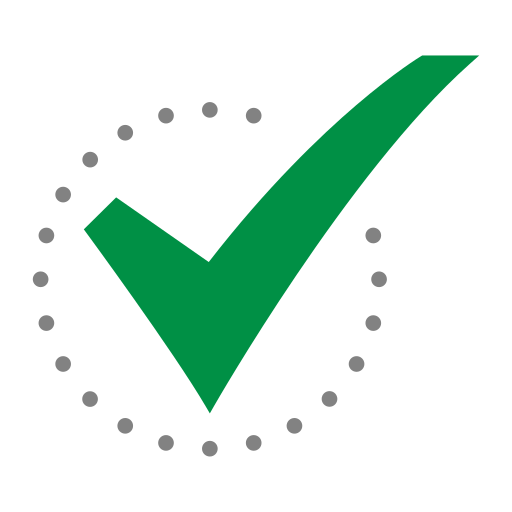
Customise and Lock fields to ensure no alteration by third-parties
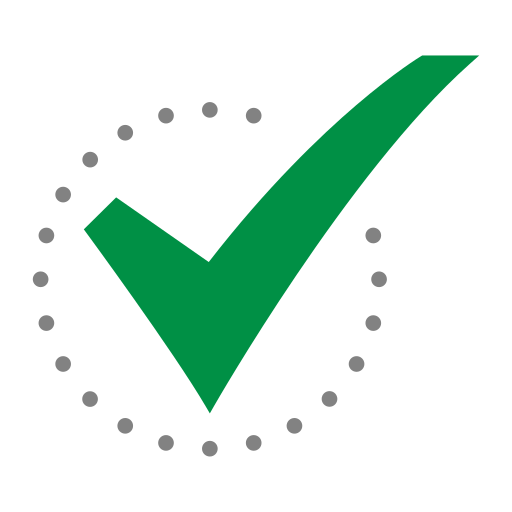
ISO 8000 International Data Quality standards built in
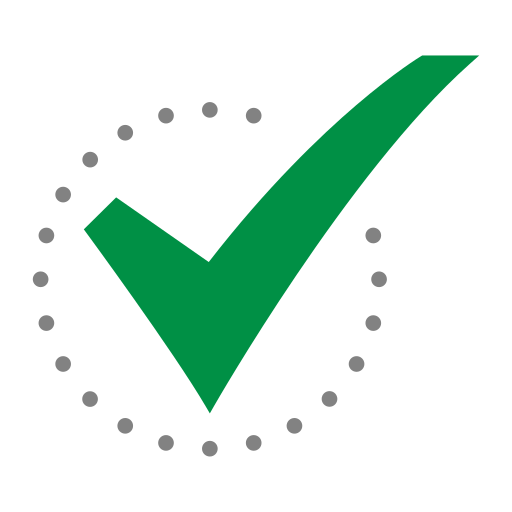
Real-time data quality measurement
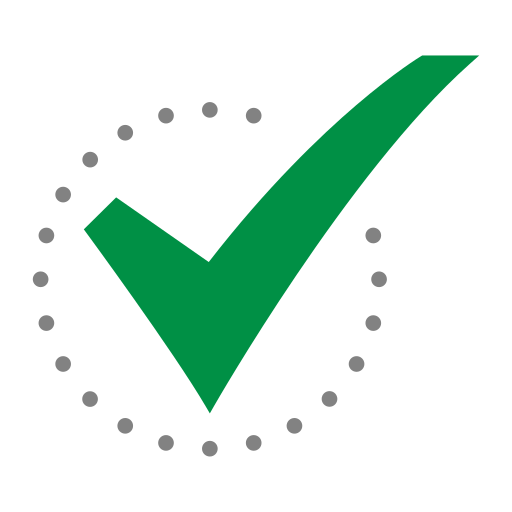
Real-time data handover
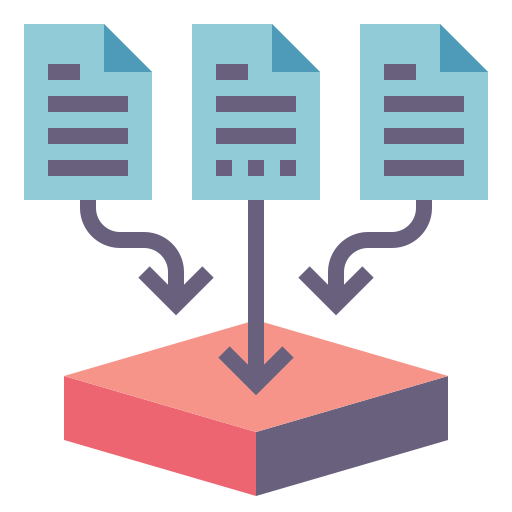
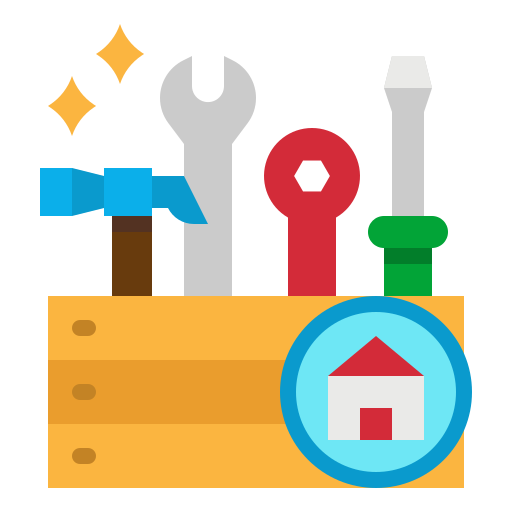
Operational support made easy
Include your maintenance strategy information such as equipment criticality and the response to failure to support the projects spares purchasing decisions
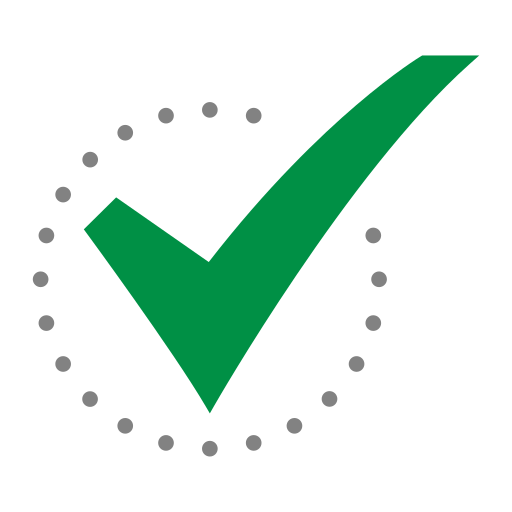
Early access to data for reliability and maintenance teams
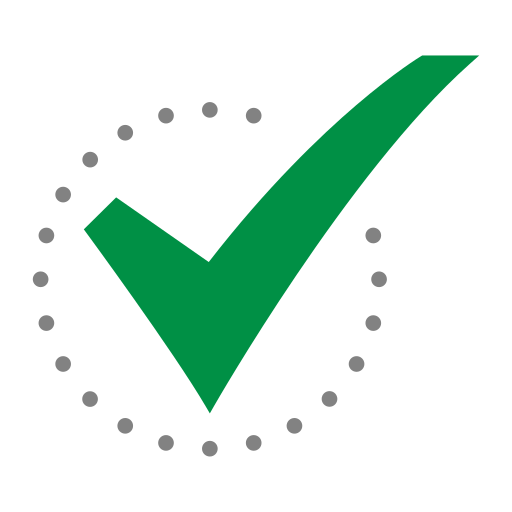
Asset criticality can be added to the equipment/tag
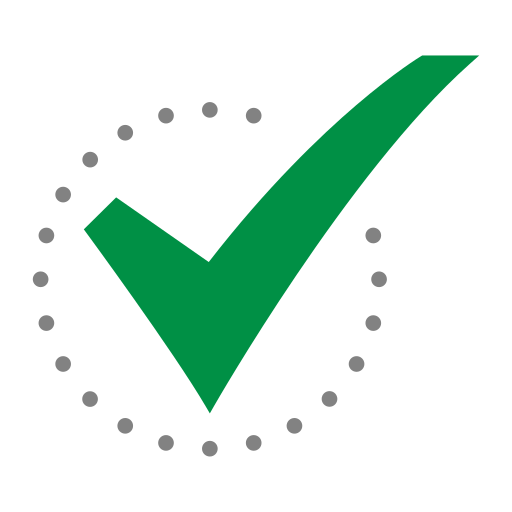
Maintenance strategy can be added to inform decision making
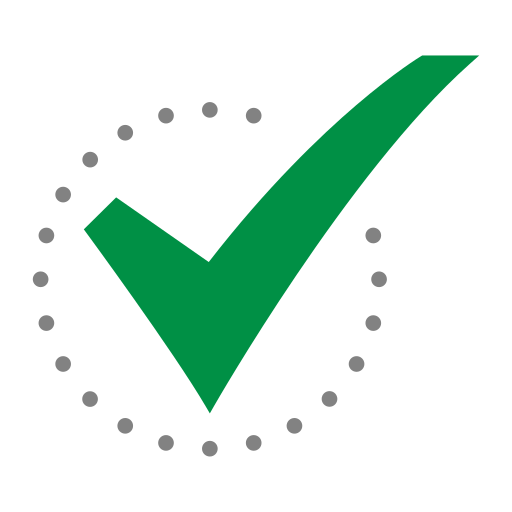
Spares review by equipment class, criticality and more
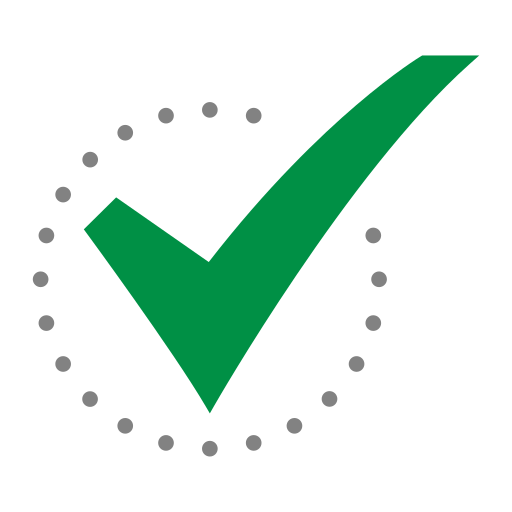
Creation of maintenance bills of material (M-BoM) for greenfield and brownfield projects
Data governance made easy
The governed spare parts data generated from SPIR documents can form the foundations for new Material Master Data or it can be mapped to your existing material masters
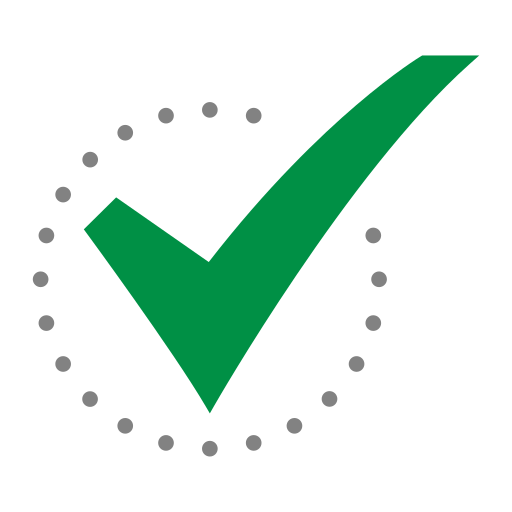
Data governance process built in
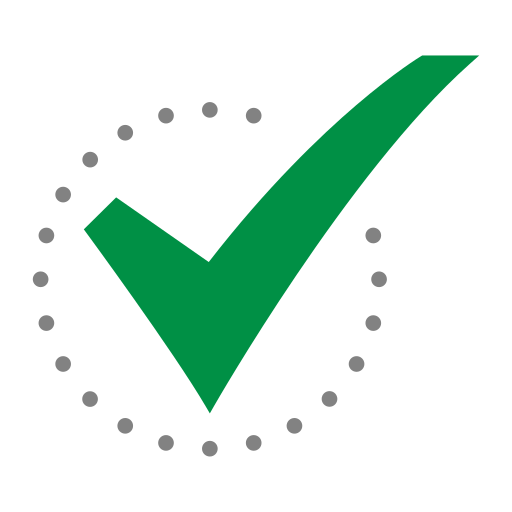
Required spares can be linked to existing material master records
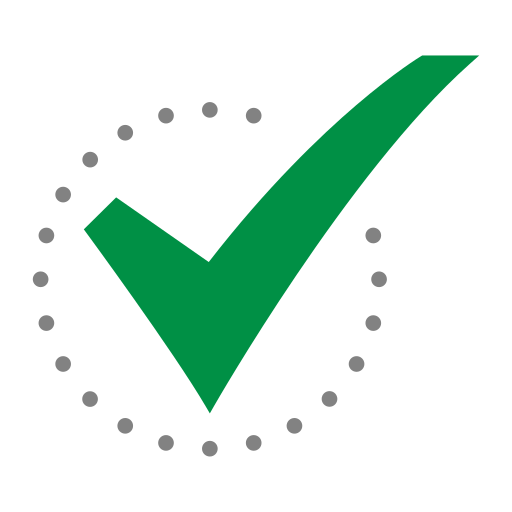
OEM descriptions can be linked to parts manufacturer descriptions
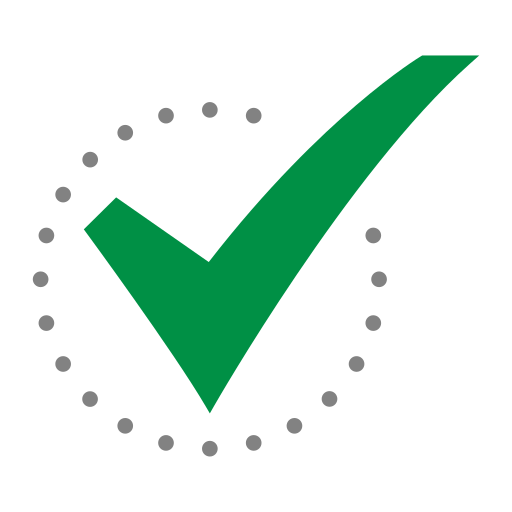
Elimination of duplicate records
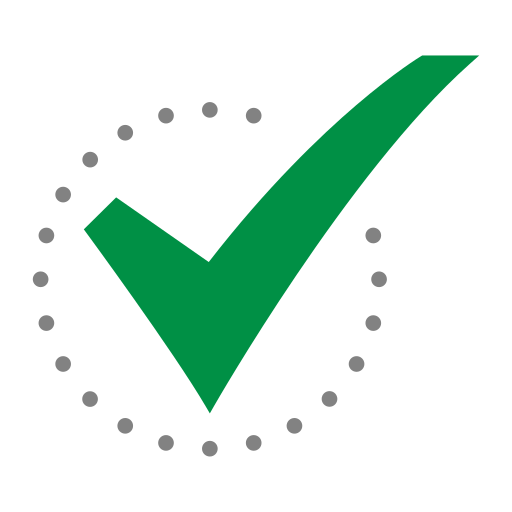
API export to existing systems
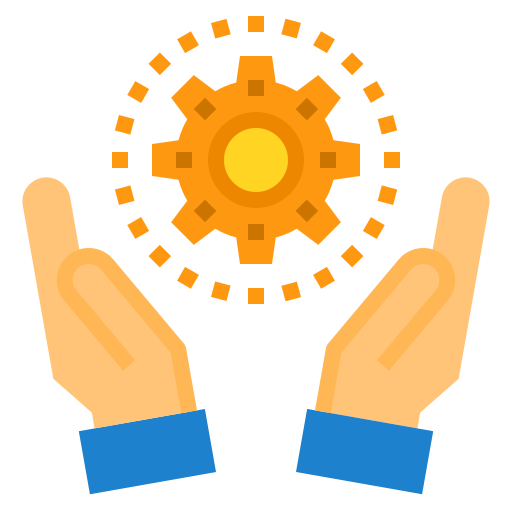
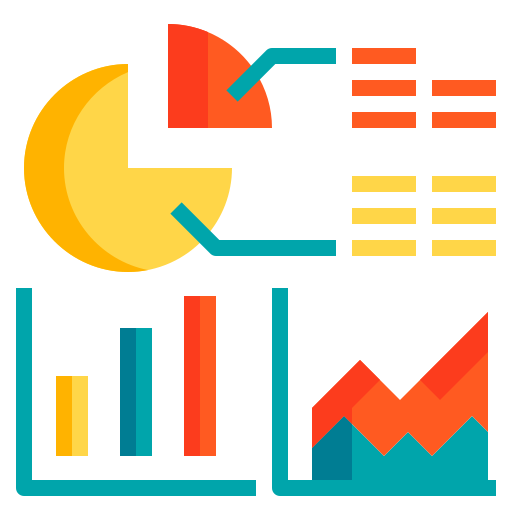
Real-time Analytics made easy
Analyse and report on your spare parts data across all SPIR documents in the project, including the cost of recommended spares
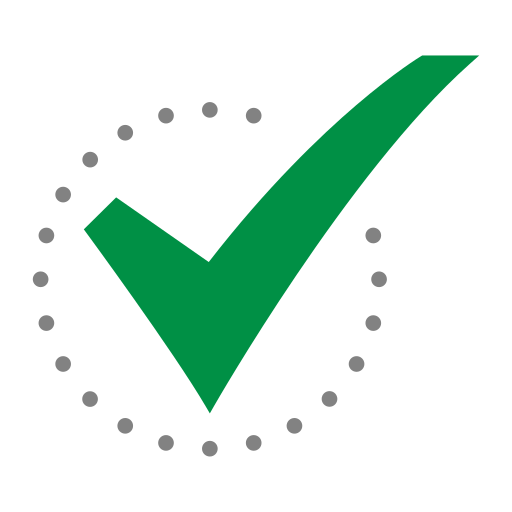
Real-time analytics
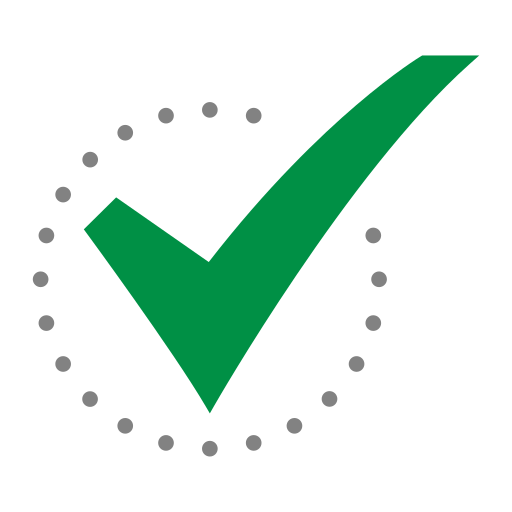
Live data quality measurement at SPIR level
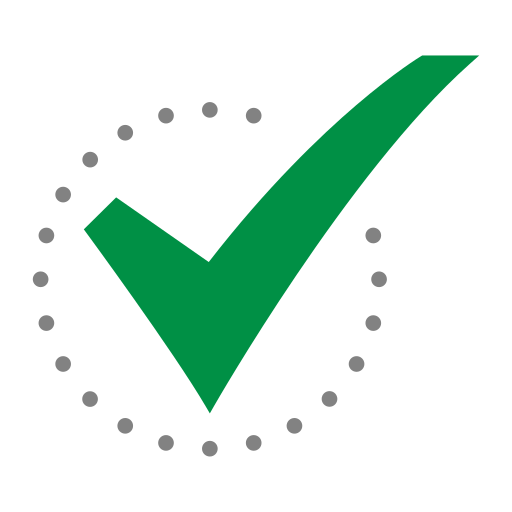
Live recommended spares cost at SPIR level, OEM level, and project level
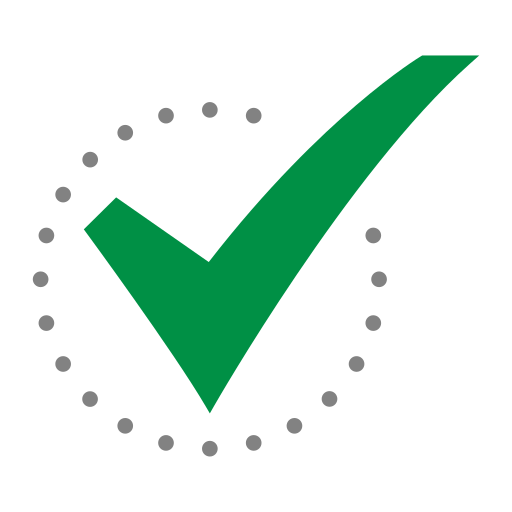
Live data quality measurement as Material Master level
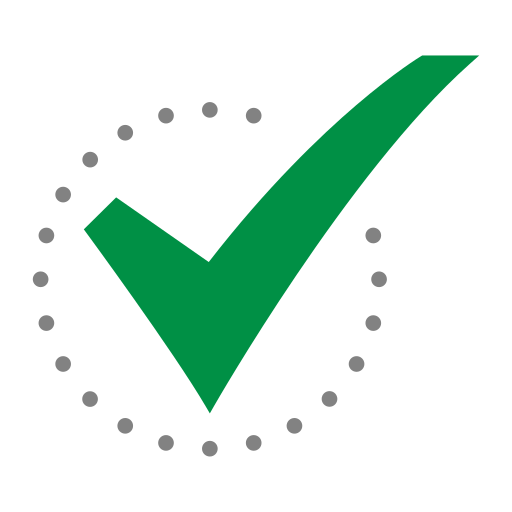
Bespoke analytics based on Owner/Operator requirements
CapEx and OpEx is reduced by streamlining the SPIR process and improving data quality
Purchasing unnecessary spares wastes money. Our software provides visibility into the SPIR process that is not possible with the traditional process, whilst improving material master data quality.
Increased visibility allows purchasing decisions, during the capital phase, to be better informed which reduces unnecessary purchases. Improving your material master data quality reduces maintenance costs during the operating phase.
Read more about how to improve your Spare Parts data
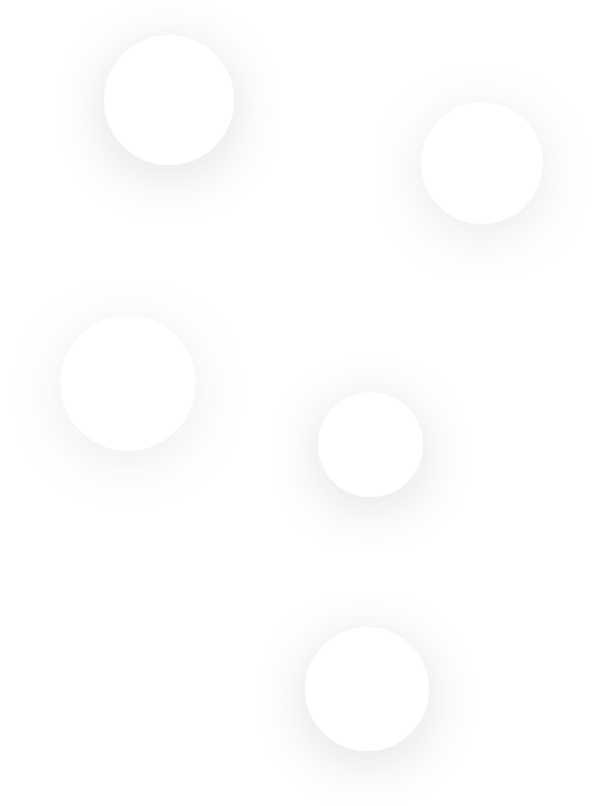
How it works
Our cloud based platform provides a single place to streamline the SPIR process
We have a deep understanding of the SPIR process. Using that knowledge, we have developed a simple, efficient and practical solution. All whilst improving the quality of the material master data created
1. Create your project
Create a project on our cloud platform and invite Engineering Procurement Contractors and Data teams to join the project
3. Upload equipment data
Upload the equipment/tag data onto the platform as the capital project evolves and tag numbers are assigned
5. Report on progress
Report on the progress of every SPIR document in real time, allowing complete transparency and continuous document handover
7. Add repairs strategy
Add fields to capture your repair or maintenance strategy, so that this information is accounted for when making purchasing decisions
2. Define your document
Select the fields you require for the entire SPIR document. Create list of values and control data types to govern the data
4. Assign SPIRs to OEMs
Group equipment/tags together into different SPIR documents and invite Equipment Manufacturers to populate the document
6. Analyse spare parts data
Analyse and report on the spare parts data including on the cost of the recommended spares and the completeness of individual fields
8. Create material masters
Create new material master records from the spare parts data or link the new records to existing material masters in your ERP system
1. Create your project
Create a project on our cloud platform and invite Engineering Procurement Contractors and Data teams to join the project
2. Define your document
Select the fields you require for the entire SPIR document. Create list of values and control data types to govern the data
3. Upload equipment data
Upload the equipment/tag data onto the platform as the capital project evolves and tag numbers are assigned
4. Assign SPIRs to OEMs
Group equipment/tags together into different SPIR documents and invite Equipment Manufacturers to populate the document
5. Report on progress
Report on the progress of every SPIR document in real time, allowing complete transparency and continuous document handover
6. Analyse spare parts data
Analyse and report on the spare parts data including on the cost of the recommended spares and the completeness of individual fields
7. Add repairs strategy
Add fields to capture your repair or maintenance strategy, so that this information is accounted for when making purchasing decisions
8. Create material masters
Create new material master records from the spare parts data or link the new records to existing material masters in your ERP system
Get in touch or book a demo
If you want to book a demonstration of our software, or if you have any questions, then please complete the form or email us directly at info@koiosmasterdata.com
SPIR articles
Introduction to SPIR challenges
In capital projects generally, and in the oil and gas upstream sector in particular, the transition from engineering design to operational readiness hinges significantly on the accurate and timely...
The SPIR process urgently needs to enter the 21st century
At KOIOS Master Data, our in-depth understanding of the SPIR (Spare Parts Interchangeability Record) process challenges comes from extensive MRO (Maintenance, Repair, and Operations) consultancy...
Understanding the risks of an inadequate spares strategy
The Hidden Costs of MRO Management Most production environments, particularly those in asset-intensive industries, rely heavily on Maintenance, Repair, and Operations (MRO) resources to keep crucial...
What is the hidden cost of holding inventory?
To accurately assess the true expense of inventory management, it's essential to consider the Inventory Carrying Cost (ICC) or Holding Cost Factor (HCF). The HCF encapsulates the financial...
How to calculate the correct spares holding in a maintenance environment
Effective materials management hinges on two essential and related components. First, understanding and recording your equipment failure responses at the equipment class level—or ideally, at the...
Is your MRO inventory culture just-in-case or just-in-time?
Corporate MRO (Maintenance, Repair, and Overhaul) inventory strategies range from "just-in-case" to "just-in-time," each carrying risks at their extremes. Finding a balance that aligns with an...