How to calculate the correct spares holding in a maintenance environment
Effective materials management hinges on two essential and related components. First, understanding and recording your equipment failure responses at the equipment class level—or ideally, at the asset or functional or location tag level, and second, establishing and maintaining an active Bill of Materials function.
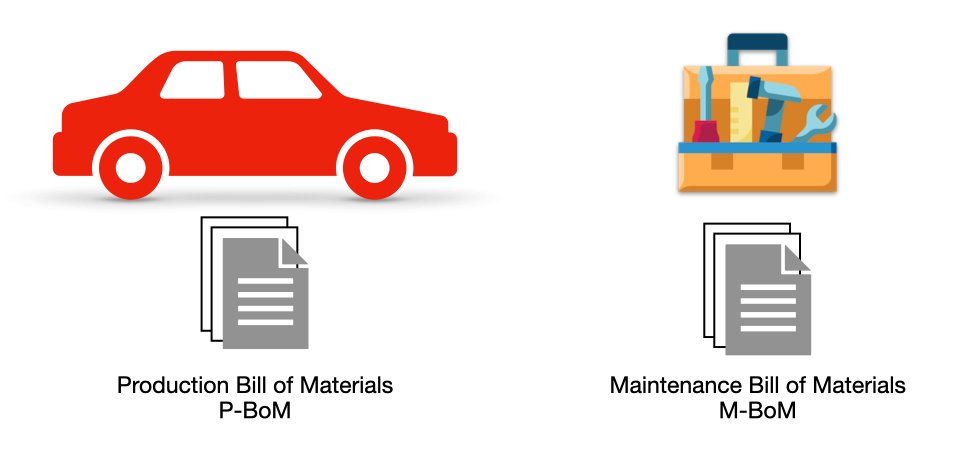
These components are inseparable. The Maintenance Bill of Materials (M-BoM) is shaped by the demand required to promptly restore equipment following a failure. The supply side, influenced by supply chain responses, is documented within the M-BoM, which depending on the cost characteristics of the equipment may include:
— A complete unit for replacement rather than repair (Rotable or Expendable equipment types);
— Internal parts for item repairs (Repairable equipment type);
— Peripheral parts, such as belts or couplings, for specific failure modes;
— Consumables like fasteners or shims, necessary for replacement post-repair;
— Special tooling.

Calculating your spares holding: A guide
Timely access to spare parts is vital for preventing significant production losses and avoiding unnecessary costs. Conversely, excessive or irrelevant inventory can tie up capital, occupy space, and inflate operating costs.
Determining the appropriate spares holding requires alignment with your facility’s maintenance strategy, incorporating principles like:
— On-site spare parts storage should be limited to field-replaceable items for critical equipment.
— Spare parts for non-critical equipment are typically not owned by the company and are ordered as needed.
— High-usage consumables may be managed through consignment stock or daily delivery from suppliers.
— Complete spare units should be stocked when cost-effective or necessary to minimize production downtime.
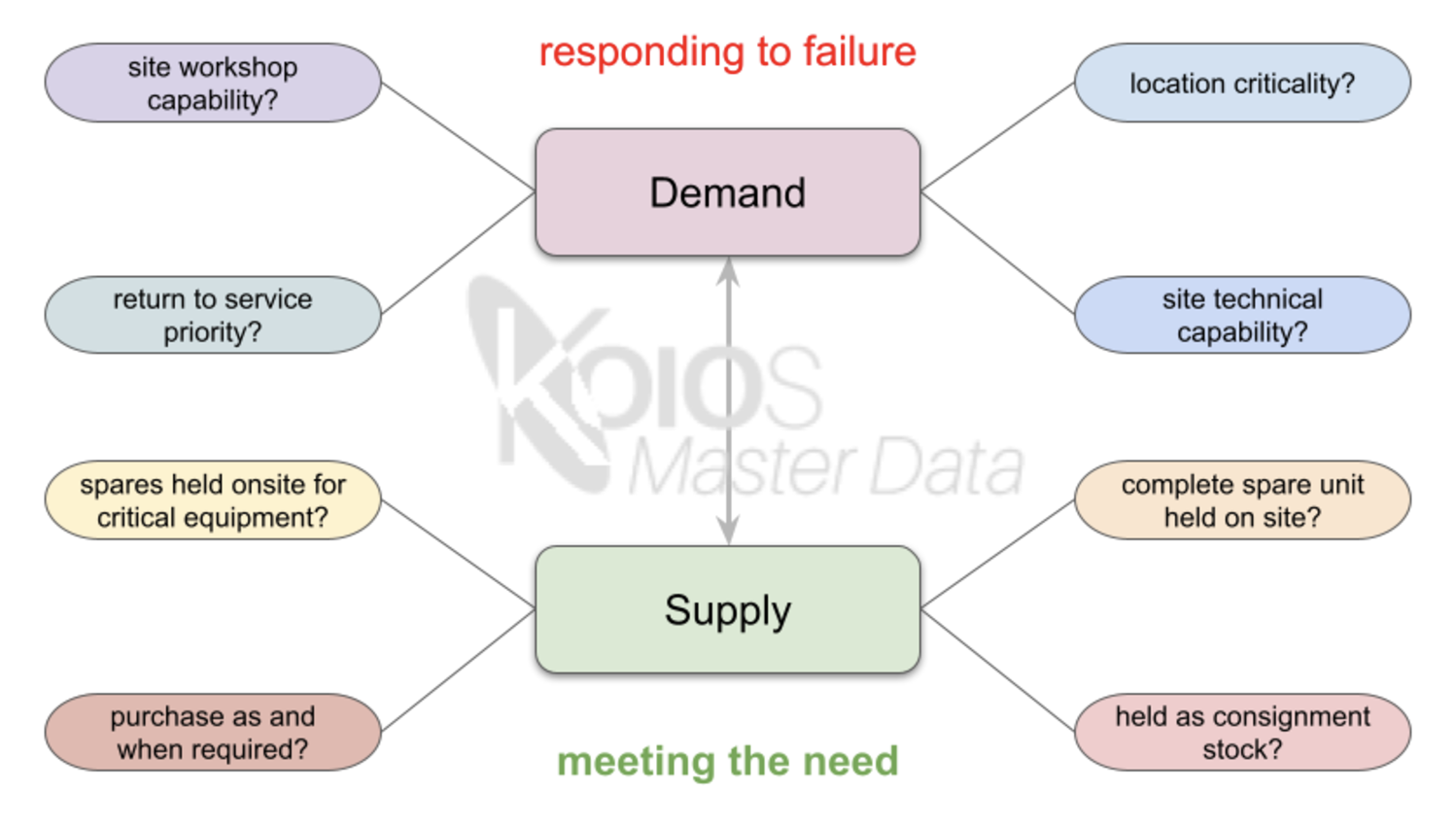
Optimizing equipment repair strategies
An effective repair strategy aligns production, maintenance, warehousing, supply chain, and finance objectives, ensuring materials stored are directly relevant to maintenance practices. This approach aims to:
— Align objectives across operations, maintenance, and logistics.
— Identify optimal repair and inventory strategies.
— Maximize working capital efficiency.
— Reduce repair times through logistical efficiency and available spares.
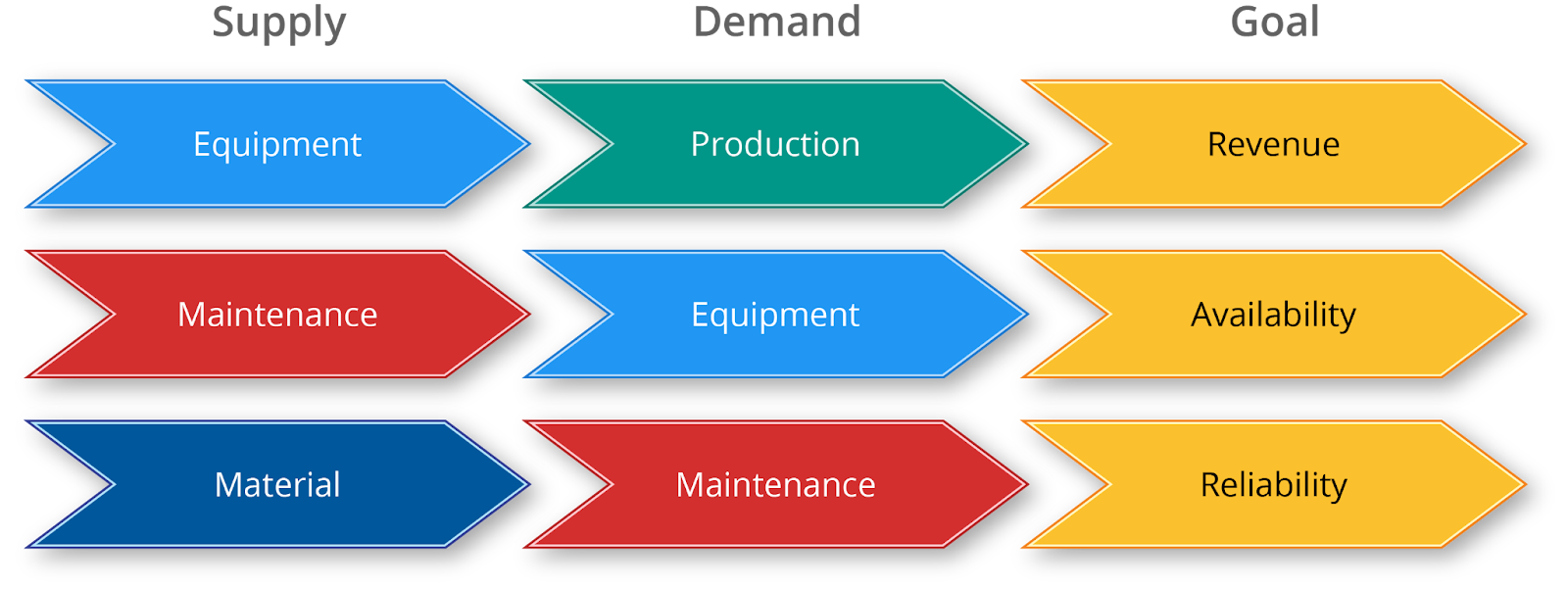
Assessing spare parts demand
Overstocking often results from initial stocking based on equipment supplier recommendations without considering site-specific factors. A tailored approach, taking into account maintenance capability, equipment criticality, and service downtime, is crucial for efficient spare parts management.
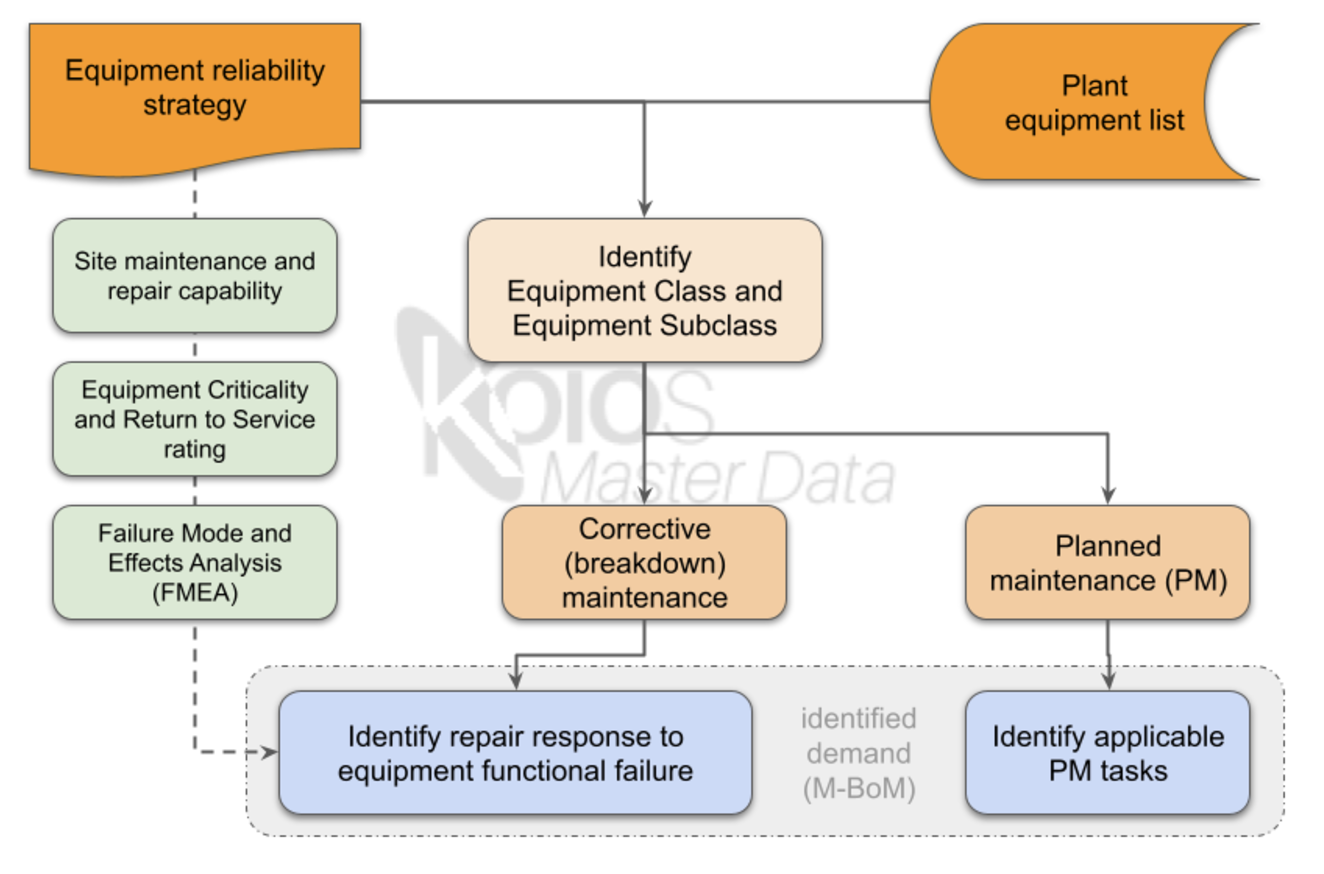
Aligning spare parts supply with demand
The lack of coordination between maintenance and stores functions can result in unavailability of necessary spare parts and accumulation of unused inventory. Adopting a “just in time” material philosophy, as opposed to “just in case,” can improve cash flow and ensure materials are available when required.
This integrated strategy aligns asset and material management objectives, ensuring materials are relevant and available to meet maintenance demands, thus ensuring the production assets perform to their maximum capacity.
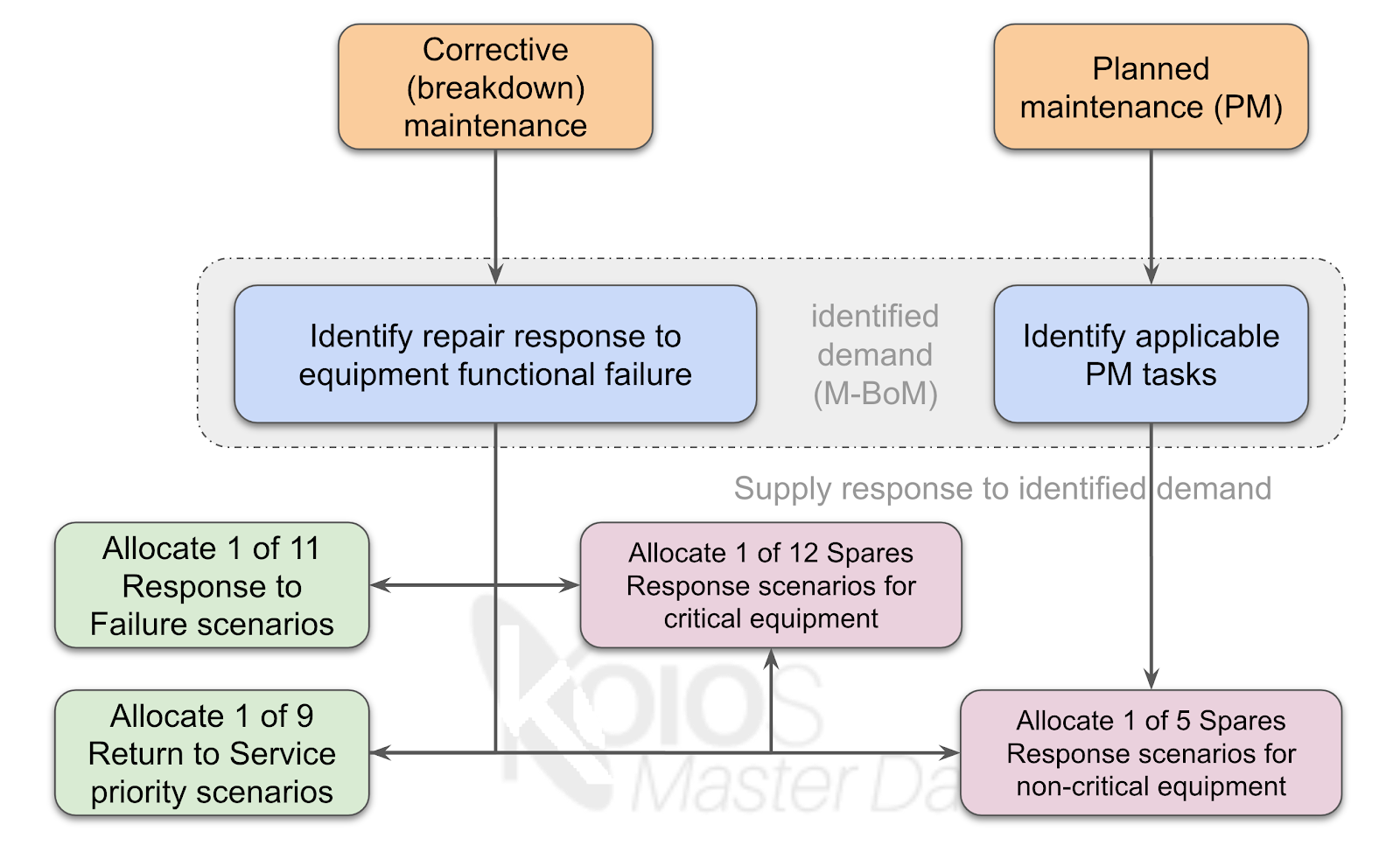
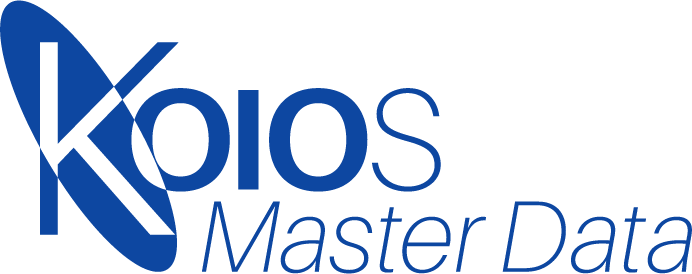
Contact us
KOIOS Master Data are experts in this field. Give us a call and find out how we can help you.
+44 (0)23 9434 0000