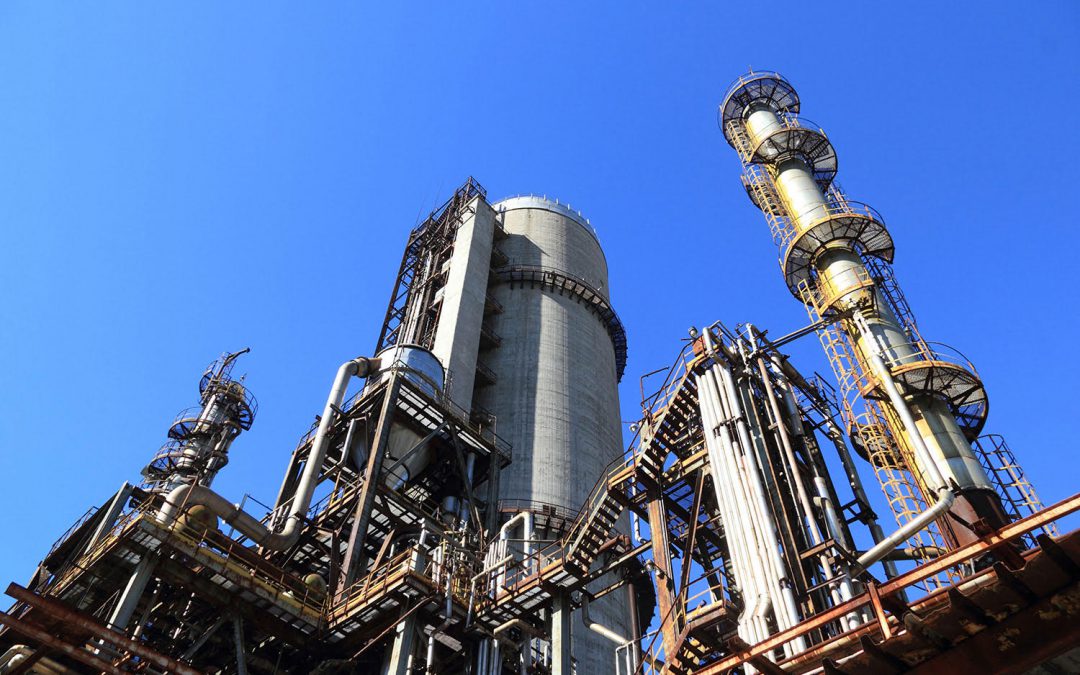
The Importance of Maintenance Bills of Material
The Importance of Maintenance Bills of Material
Introduction to the M-BoM
Maintenance Bills of Material (M-BoM) are pivotal in distinguishing “best in class” facilities from their counterparts. These documents are integral for facilities committed to operational excellence, yet surprisingly absent or incomplete in many organizations.
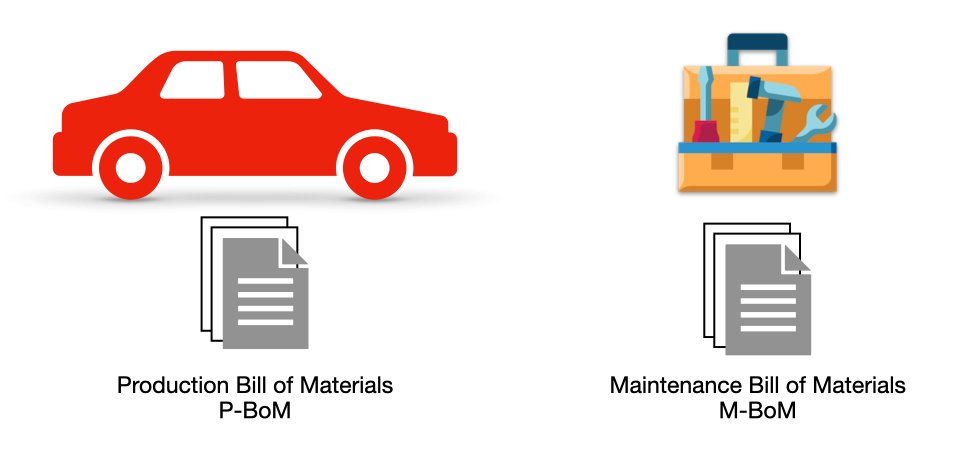
The role of the M-BoM in operational efficiency
Facilities without M-BoMs often face challenges from the outset, with many operating for years without them. The lack of M-BoMs is frequently attributed to unavailable data or resources, perpetuating inefficiency through workaround practices.
The Impact of Not Having an M-BoM
The consequences of operating without an M-BoM program are significant, leading to escalated failure costs and unnecessary inventory expenses. A comprehensive M-BoM should cover complete units, internal and peripheral parts for repairs, and consumables.
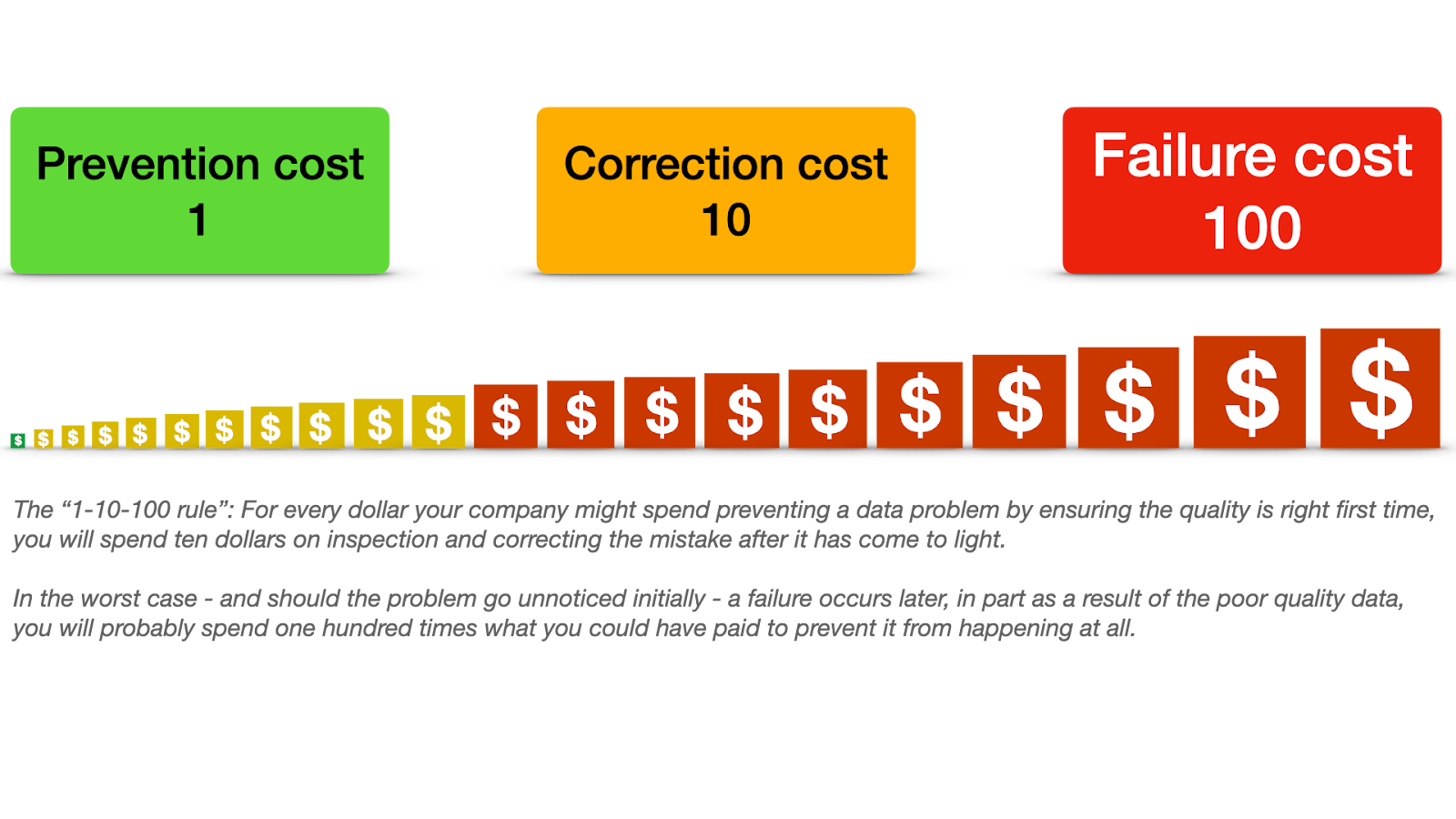
The “1-10-100 rule” (Labovitz, Chang) as it applies to the impact of not having M-BoMs can be expressed as follows:
“For every dollar your company might spend preventing a data problem by ensuring the quality is right first time, you will spend ten dollars on inspection and correcting the mistake after it has come to light.
In the worst case – and should the problem go unnoticed initially – a failure occurs later, in part as a result of the poor quality data, you will probably spend one hundred times what you could have paid to prevent it from happening at all”.
Key success factors for an M-BoM
Effective M-BoM management involves early data integration, alignment with failure response, robust processes for technical upgrades and managing retired assets, and a culture that values accurate M-BoMs.
Bills of Material in SAP Plant Maintenance (PM)
There are three main categories of a maintenance BoM in SAP PM:
- Material BoM;
- Equipment BoM
- Functional Location BoM.
Note: The following information is for guidance only. The information is taken from available SAP published information at the time of writing. Your own system may have a different configuration.
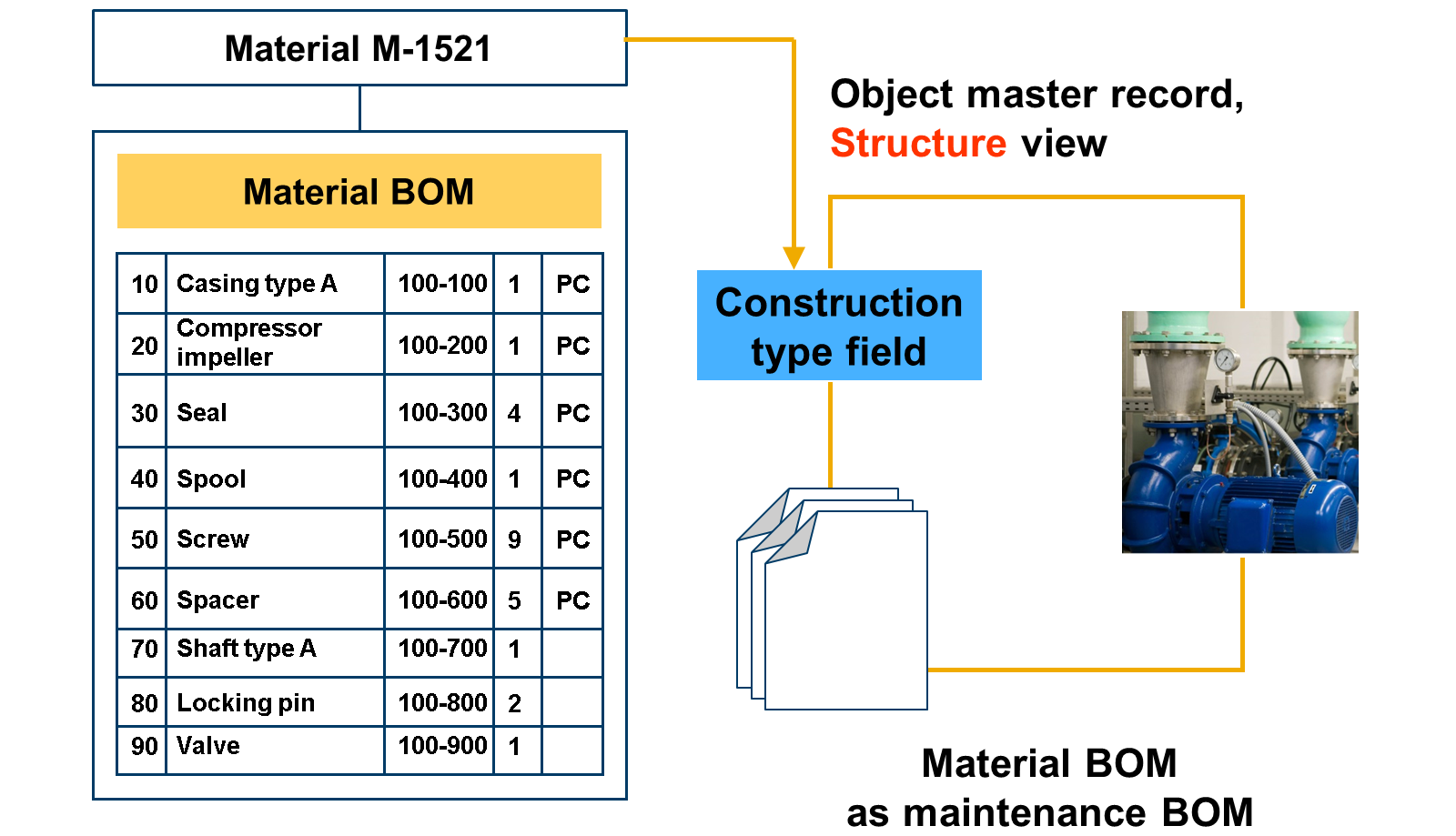
SAP Plant Maintenance tailors M-BoM for specific maintenance needs, offering structured maintenance planning and efficiency through categorized M-BoMs like Material, Equipment, and Functional Location BoMs. This system aims to streamline maintenance tasks and reduce redundancy.
What function does and M-BoM perform
The maintenance BoM performs the following important functions:
- Structuring of the object. The structure of an object must be displayed as clearly as possible from a maintenance viewpoint;
- Spare parts planning in an order. If a technical object uses a BoM, you can use this during the planning or maintenance order to plan spare parts;
- Spare parts planning in the task list. Spare parts can be planned in the task list based M-BoM
Material BoMs are always used in SAP PM if a number of identically constructed objects have to be maintained. The aim is not to create a M-BoM for each technical object, but to create just one M-BoM, and then assign this to the relevant technical objects. This avoids the use of redundant M-BoMs.
The procedure for creating a material BoM is as follows:
- Create a material.
- Create a material BoM for the material
The M-BoM must then be assigned to one or more technical objects such as equipment or functional location. You can make the assignment or assignments in the respective master record by using the Structure view.
SAP transactions for BoMs
SAP M-BoM transactions codes include:
- CS01, CS02, CS03 – Create, Change, Display Material BoM);
- IH05 – Structural Display Material BoM
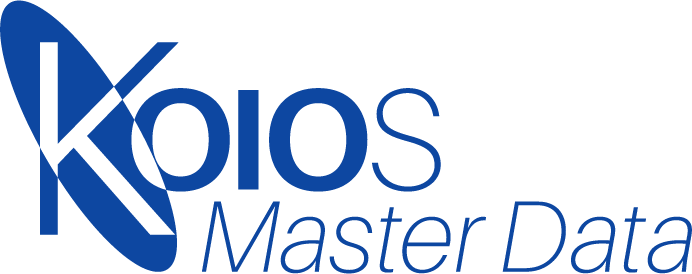
Contact us
KOIOS Master Data are experts in this field. Give us a call and find out how we can help you.
+44 (0)23 9434 0000